AS尾氣系統(tǒng)設(shè)備腐蝕的原因及解決措施
羅小林 吳恒喜 肖建軍 王凱軍 路 遙(武漢平煤武鋼聯(lián)合焦化公司,武漢430082)
1 AS工序現(xiàn)狀及存在問(wèn)題
武鋼聯(lián)合焦化公司從德國(guó)史梯爾公司引進(jìn)了1套AS脫硫工藝,AS脫硫工藝是脫硫、脫氨、脫酸和蒸氨的總稱。其中硫化氫和氰化氫的脫除是利用煤氣中的氨作為堿源,用洗氨后的富氨水吸收煤氣中的酸性氣體硫化氫、氰化氫和二氧化碳等,該富液水送脫酸塔脫除含硫化氫、氰化氫和氨汽的酸性氣體,硫化氫在克勞斯?fàn)t中最終生成為單質(zhì)硫,氨分解為N2和H2。硫化氫和氨分解后的尾氣經(jīng)循環(huán)氨水洗滌后送初冷器前。AS工藝流程見(jiàn)圖1。
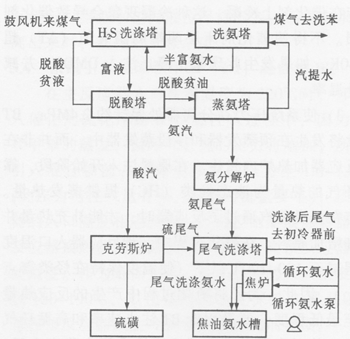
圖1 武鋼AS系統(tǒng)及尾氣處理工藝流程圖
AS工藝的最大優(yōu)點(diǎn)是脫硫的洗滌劑本身為焦?fàn)t煤氣的一種組分,不必外購(gòu)洗滌劑。經(jīng)過(guò)AS工序處理后的煤氣中的硫化氫含量可達(dá)500mg/m3以下,但普遍存在生產(chǎn)設(shè)備和工藝管道腐蝕嚴(yán)重的問(wèn)題。對(duì)于該工藝腐蝕的原因雖然進(jìn)行了研究,但一直沒(méi)有找出確切的原因和很好的解決辦法。
2 AS工序設(shè)備腐蝕原因
武鋼AS系統(tǒng)腐蝕最嚴(yán)重的部位是AS系統(tǒng)尾氣管道和循環(huán)氨水管道,武鋼沒(méi)有AS系統(tǒng)的煤氣回收工藝,氨水管道非常耐用,只有AS系統(tǒng)的循環(huán)氨水管道腐蝕嚴(yán)重,其唯一差別就是AS系統(tǒng)使用循環(huán)氨水對(duì)尾氣進(jìn)行洗滌凈化處理。由此可知,AS系統(tǒng)產(chǎn)生的腐蝕主要是尾氣腐蝕,必須找出腐蝕的原因。
2.1 硫化氫氣體分解生成的腐蝕性物質(zhì)
武鋼AS系統(tǒng)產(chǎn)生的硫化氫氣體其濃度為15%~25%,硫化氫氣體的濃度較低,反應(yīng)熱量不足,難以維持燃燒爐內(nèi)克勞斯反應(yīng)所要求的溫度,所以將1/3的酸性氣體送入燃燒爐與適量空氣燃燒生成SO2 ,生成的SO2與未進(jìn)入燃燒爐的其余酸性氣體一起進(jìn)入轉(zhuǎn)化器進(jìn)行低溫催化反應(yīng),所以采用了分流法。分流法一般設(shè)計(jì)成二級(jí)催化反應(yīng)器的工藝,硫化氫的總轉(zhuǎn)化率可達(dá)89%~92%。轉(zhuǎn)化的主要反應(yīng)化學(xué)方程式如下:
2H2S+O2 = 2S+2H2O (1)
2H2S+3O2 = 2SO2+2H2O (2)
2H2S+SO2 = 3S+2H2O (3)
只要空氣和酸性氣體的比例適當(dāng),那么克勞斯?fàn)t燃燒的尾氣中就基本上沒(méi)有過(guò)多的SO2生成??刂莆矚馐欠襁^(guò)氧的主要手段是采用需氧分析儀。需氧分析儀本身存在調(diào)整問(wèn)題,控制是否過(guò)氧還需要人工化驗(yàn)作為輔助手段,利用尾氣中二氧化硫的含量數(shù)據(jù)。由于只依靠需氧分析儀進(jìn)行調(diào)節(jié),所以過(guò)氧狀況波動(dòng)非常大,尾氣中SO2的含量最高時(shí)達(dá)到50g/m3。 2008年1~11月,尾氣中SO2的含量波動(dòng)見(jiàn)圖2。
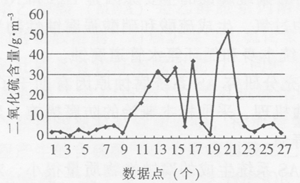
圖2 尾氣中SO2含量的波動(dòng)情況
從圖2可看出,克勞斯反應(yīng)中空氣量控制不好,在局部時(shí)間段空氣過(guò)量嚴(yán)重,過(guò)量的空氣不僅促成反應(yīng)(2)生成更多的SO2,而且SO2會(huì)與O2繼續(xù)反應(yīng)生成SO3,其反應(yīng)式如下:
2SO2+O2 = 2SO3 (4)
在克勞斯?fàn)t反應(yīng)器中,大量生成SO2和SO3 , SO2和SO3又溶于稀氨水中生成稀硫酸和亞硫酸,其化學(xué)反應(yīng)方程式如下:
SO2+H2O = H2SO3 (5)
SO3+ H2O = H2SO4 (6)
為了驗(yàn)證以上推理,安排AS系統(tǒng)的循環(huán)氨水和沒(méi)有煤氣脫硫的循環(huán)氨水做硫酸根離子濃度檢測(cè)。檢測(cè)發(fā)現(xiàn),用循環(huán)氨水洗滌尾氣的氨水中的硫酸根離子濃度為149.17mg/L,沒(méi)有脫硫的煤氣回收系統(tǒng)循環(huán)氨水中的硫酸根濃度檢測(cè)不出,證明尾氣洗滌系統(tǒng)把強(qiáng)酸洗滌下來(lái)。除部分硫酸和亞硫酸與氨水中的氨生成銨鹽外,大部分成游離酸狀態(tài),對(duì)設(shè)備造成極大腐蝕。
2.2 氨汽分解生成的腐蝕性物質(zhì)
氨在1000~1200℃的高溫下會(huì)發(fā)生分解反應(yīng),生成N2和H2,此反應(yīng)是吸熱反應(yīng)。為了保持最佳的反應(yīng)溫度,必須補(bǔ)充一定量的焦?fàn)t煤氣和空氣,通過(guò)煤氣的燃燒熱維持氨分解反應(yīng)所需的溫度,由于煤氣燃燒和氨汽中酸性氣體參與反應(yīng),反應(yīng)過(guò)程十分復(fù)雜,其主要反應(yīng)式為:
2NH3 = N2+3H2 (7)
2HCN+2H2O = 2CO+N2+3H2 (8)
CH4+2O2 = CO2+2H2O (9)
2H2+O2 = 2H2O (10)
除了產(chǎn)生以上的主反應(yīng),在鉑或者氧化鐵存在的情況下,氨很容易和氧發(fā)生如下反應(yīng):
4NH3+O2 = 4NO+6 H2O (11)
NO不溶于水,容易和氧化合生成NO2, NO2易溶于水生成HNO3和NO。其化學(xué)反應(yīng)方程式如下:
3NO2+H2O = 2HNO3+NO (12)
所以,在氨的分解過(guò)程中,式(11)和式(12)這兩個(gè)副反應(yīng)生成的物質(zhì)是稀硝酸,它具有極強(qiáng)的腐蝕性。
對(duì)氨尾氣進(jìn)行的檢測(cè)發(fā)現(xiàn),其含氧為700mg/m3,含CO 2100mg/m3。因檢測(cè)出氧的存在,故具備了生成硝酸的條件。為了驗(yàn)證AS系統(tǒng)能生成更多硝酸根離子,對(duì)3個(gè)煤氣回收系統(tǒng)的循環(huán)氨水進(jìn)行了NO2-、 NO3一濃度化驗(yàn)對(duì)比,檢測(cè)結(jié)果見(jiàn)表1。
表1 煤氣回收系統(tǒng)循環(huán)氨水中NO2-、 NO3一濃度(mg/L)
煤氣回收系統(tǒng) |
NO2-濃度 |
NO3一濃度 |
備注 |
一回收系統(tǒng) |
0 |
1.27 |
沒(méi)有AS系統(tǒng) |
二回收系統(tǒng) |
0 |
1.38 |
AS系統(tǒng) |
三回收系統(tǒng) |
0 |
1.01 |
沒(méi)有AS系統(tǒng) |
從檢測(cè)結(jié)果可看出,AS系統(tǒng)生成了更多NO3一, 它對(duì)設(shè)備的腐蝕很大。如果生產(chǎn)處于不正常狀態(tài)或者調(diào)試階段,尾氣中的NO3一濃度會(huì)更高,對(duì)設(shè)備的腐蝕作用會(huì)更強(qiáng)烈。
3 AS尾氣系統(tǒng)防腐措施及改進(jìn)
3.1 AS尾氣系統(tǒng)防腐措施
在硫化氫等酸性氣體和氨汽的分解過(guò)程中生成的腐蝕性氣體,如果直接留在煤氣中會(huì)對(duì)煤氣管道造成極大腐蝕。武鋼聯(lián)合焦化公司對(duì)這些處理后的尾氣經(jīng)氨水洗滌后再送入初冷器前,通過(guò)循環(huán)氨水把尾氣中的腐蝕性物質(zhì)洗滌下來(lái),煤氣管道的腐蝕得以控制。為了檢測(cè)洗滌效果,對(duì)經(jīng)過(guò)AS系統(tǒng)處理的煤氣進(jìn)行硫和氮的氧化物檢測(cè),結(jié)果沒(méi)有檢出,證明尾氣洗滌效果明顯。為進(jìn)一步驗(yàn)證煤氣管道的腐蝕物質(zhì),武鋼鋼研所進(jìn)行了煤氣管道腐蝕性殘留物X射線衍射分析,檢測(cè)結(jié)果見(jiàn)圖3。
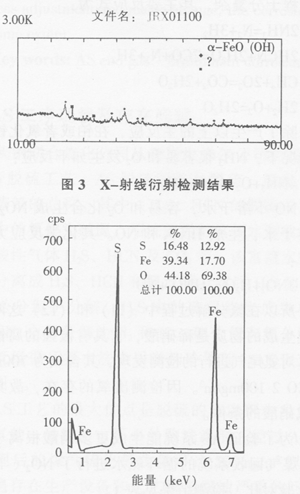
圖4 電子探針?lè)治鰣D
根據(jù)衍射圖譜分析,其主要物相為α-FeO(OH),少量的未知相疑為硫。為了解脫落物的組成,進(jìn)行了電子探針成分分析,結(jié)果見(jiàn)圖4。探針?lè)治鼋Y(jié)果表明,沉積物主要為Fe、O、 S。
根據(jù)分析結(jié)果推算,煤氣管內(nèi)沉積物中的70%左右為α-FeO(OH),同時(shí)還有元素硫。說(shuō)明沉積物主要是煤氣管道的腐蝕產(chǎn)物,為煤氣中硫化氫腐蝕的結(jié)果。這說(shuō)明AS系統(tǒng)煤氣中的強(qiáng)酸性物質(zhì)被氨水完全洗滌,雖然煤氣管道得到了保護(hù),但隨著污染物的轉(zhuǎn)移,造成氨水管道嚴(yán)重腐蝕。
3.2 AS尾氣系統(tǒng)防腐改進(jìn)建議
為將腐蝕程度降到最低,建議采取如下改進(jìn)措施:
1) 控制生產(chǎn)操作參數(shù)。對(duì)克勞斯反應(yīng)的尾氣進(jìn)行控制,增加尾氣中SO2和H2S的日常化驗(yàn)數(shù)據(jù),將硫尾氣中的SO2和H2S含量確定為≤3000mg/m3,以確保不過(guò)氧,且H2S轉(zhuǎn)化完全。增加氨尾氣中的CO和O2的日?;?yàn)數(shù)據(jù),并限定CO含量大于500 mg/m3,氧含量為零。這兩個(gè)參數(shù)極為關(guān)鍵,它能確保不生成或者少生成強(qiáng)腐蝕性物質(zhì)硝酸。只有控制好硫和氨尾氣的關(guān)鍵參數(shù),才能從源頭上控制腐蝕性物質(zhì)的生成。
2) 建議增加洗滌尾氣的循環(huán)氨水酸堿性檢測(cè),根據(jù)洗滌氨水的酸堿性隨時(shí)調(diào)整洗滌氨水量或添加適量堿性物質(zhì),保證酸性物質(zhì)中和完全,從而減輕強(qiáng)酸性物質(zhì)對(duì)循環(huán)氨水管道的腐蝕。
3) 對(duì)設(shè)備管線材質(zhì)進(jìn)行改造,將氨水循環(huán)管道更換為不銹鋼管道。
IV>4 結(jié)論
1) AS系統(tǒng)腐蝕的主要原因是H2S和NH3在分解過(guò)程中過(guò)氧,生成硫酸和硝酸強(qiáng)腐蝕性物質(zhì),造成AS系統(tǒng)本身和循環(huán)氨水管道腐蝕。
2) 充分研究AS系統(tǒng)腐蝕原因有助于了解AS系統(tǒng)腐蝕機(jī)理,采取標(biāo)本兼治的防腐措施,延長(zhǎng)設(shè)備使用壽命。
3) AS系統(tǒng)生成的腐蝕性物質(zhì)量很小,難以富集,化驗(yàn)復(fù)雜,難度大,有待于今后進(jìn)一步的研究。